Resins for Potting and Encapsulation in the Electronics and Electrical
Resins for Potting and Encapsulation in the Electronics and Electrical
Epoxy resins have been widely used for many years – they are generally hard and tough and exhibit low shrinkage on cure. They are characterised by an excellent level of mechanical properties, good high temperature performance and good adhesion to a wide variety of substrates, and show excellent chemical resistance across a wide range of chemicals. The cross-linking or curing process generally takes place slowly especially where small volumes of resin are involved. Fast cure hardeners can be used but these generate a lot of heat during cure, giving rise to a high exotherm which can damage electronic components and cause high mechanical stresses on both components and the circuit.
Polyurethane resins are elastomeric or rubbery in their cured state and are preferred where circuits to be potted contain delicate components such as ferrites or those with fragile legs. It is much easier to tailor the cure speed with urethane systems and the usable life and gel time of these can be adjusted to suit customer requirements, leading to faster process times and less work in progress. Generally polyurethanes show lower exotherm during cure than epoxies – the heat generated is not usually a problem, even for fast cure systems. Conventional polyurethanes can be subject to attack by water, especially at high temperatures. Polybutadiene based urethanes are available, however, and these are very resistant to water, both during the curing process and in the final cured state. Electrolube differentiate between the two types of polyurethane in the numbering system that is used – UR 50** and UR 51** materials are based on polybutadiene chemistry. UR 55** and 56** materials are based on other polymer backbones urethanes. For the majority of polyurethanes the maximum operating temperature is limited to 130°C, however recent advances have allowed the maximum operating temperature of the new generation of resins to be increased to 150°C. The ease with which the process characteristics and final properties of polyurethane resins can be varied to suit customer requirements has led to their use in a wide range of electronics and electrical encapsulation.
Silicone resins tend to be more expensive than epoxies or urethanes, but find a use where high and or low continuous operating temperatures (-50 to 200°C) are involved. Due to their inherent high flexibility makes these resins particularly suitable for applications where there is a high level of thermal shock involved, or a high frequency of thermal cycling. The amount of heat given off during the curing of silicone resins is very low indeed, making them particularly suitable for use in potting temperature sensitive components. Silicones have excellent adhesion to a wide range of substrates, including most common metals and plastics. In general silicones are soft, which means they are not as resilient as epoxy or polyurethane resins.
Polyester systems are used for potting and encapsulation, but in general they produce a very high exotherm when cured at room temperature and often a high level of shrinkage can occur on cure. This can cause component and circuit damage. Traditionally these resins have contained styrene as a reactive monomer, which has caused problems in the past due its odour and volatility, however the newer generation of resins have replaced styrene with other reactive monomers which have reduced hazards associated with them.
Electrolube offers a comprehensive range of epoxy, polyurethane and silicone resins for potting, encapsulation and other applications. The great majority of these are two part systems where a resin has to be mixed with a hardener in a defined ratio before use. Two part resin systems are available in a range of different sizes to suit customer requirements, either as bulk, kits or resin packs. The kits have the resin and hardener pre-weighed into containers in the correct ratio, thus avoiding the necessity for weighing by the user.
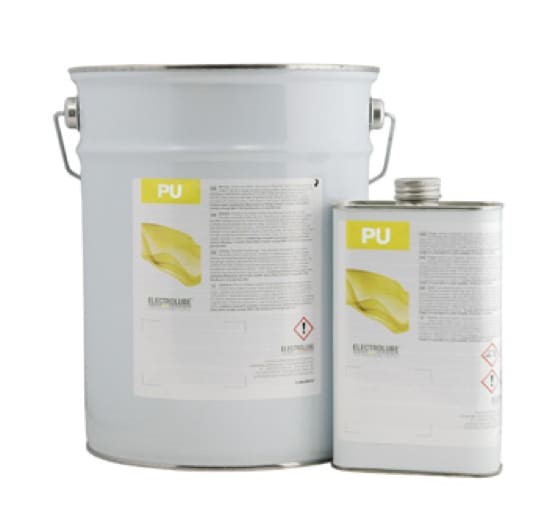
The advantage of the resin pack is that small quantities are available, the pack consists of a plastic bag divided into two compartments by a removable seal and clip. Once again the resin and hardener are in the correct ratio and also, after the seal has been removed, both parts can be thoroughly mixed in the bag without introducing air. The bag can then be used as a dispenser to pot the unit concerned. Electrolube do offer a limited range of one part epoxies which are heat cured and can be used for small encapsulations. One part moisture curing polyurethane and silicone resins are available, but moisture penetration in order to obtain full cure is a problem with potting or encapsulation. It is possible to formulate one part resins that can be cured by UV, but this technology is not well suited to formulation of potting resins because of shadow issues and the degree of cure at depth when curing thick sections with components and complicated geometries.
Most resin systems in use are complex products with process characteristics and final properties adjusted to suit customers’ needs using the skill of the formulator. Epoxy resins usually contain the base epoxy, typically bisphenol A, and diluents or viscosity reducers which can make the resin thinner and easier to process. Diluents can be reactive, taking part in the cross-linking process, or non-reactive, being chemically inert.
Reactive diluents can contain one (monofunctional) or two (difunctional) epoxy group(s) per molecule – the former give better viscosity reduction but have a larger impact upon the mechanical properties than the latter. Non-reactive diluents generally provide a better level of flexibility into the cured product, but can give rise to reduced adhesion, especially at high temperatures. Electrolube’s ER 1448 is an example of a very low viscosity epoxy resin formulated using a proprietary blend of diluents of both types – it gives rapid and efficient air displacement from small complex circuitry without the necessity for evacuating to remove entrapped air. Non-reactive diluents can be used at very high levels in polyurethanes to give soft potting compounds which can easily be removed from circuitry for fault investigation or repair. UR5048 is a popular example of such a resin while 5044 is a flame retardant version of this approved to Underwriters Laboratories UL 94 V-0.
The hardener used with the epoxy resin makes a very important contribution to final properties, and also choice of hardener is the main way of altering the speed of cure and the potential exotherm. The earliest hardeners used were a rather aggressive class of chemicals called primary aliphatic amines. These give a fast cure but a consequent high exotherm – they are corrosive to the skin and can give rise to dermatitis and asthma if not handled with care. Related to these are aromatic amines give rise to better thermal and mechanical properties in the cured product, but although they are less sensitising, they have been found to have carcinogenic and mutagenic properties, which has led to them been phased out. Amine hardeners are often supplied as complex blends of different materials, frequently as polyamides, and involve specialist formulating skills in their own right. Organic acid anhydrides give low viscosity epoxies with very high continuous operating temperatures and excellent chemical resistance, but need to be cured at high temperatures.
Polyurethane resins are generally based on the use of hydroxyl terminated polymers, often referred to as polyols. Generally polyols based on either polybutadiene or polyether backbones exhibit better water resistance but polyester based polyols show improved adhesion. The second component of the resin is an isocyanate, usually diphenyl methane diisocyanate (MDI), however since this has a distinct yellow/brown colour, for the optically clear resins aliphatic isocyanates are used. Of these over the past few years the trimer of 1,6-hexamethylene diisocyanate (HDI) has become more common due to its low hazard classification. It is important to protect both parts of the resin from moisture. If the resin component becomes wet, then the water will react with the isocyanate and produce bubbles of carbon dioxide gas throughout the cured product. If the isocyanate becomes wet, a solid deposit will be produced within the material (urea), together with carbon dioxide gas, which may pressurize the can. The usual cause of wet resin or hardener is repeated opening and closing of the containers – each time the container is opened moist air enters the air space above the liquid, and the water is absorbed into the material. Containers should be opened and closed as quickly as possible – flushing the can with dry nitrogen before closing will help prevent problems. If this is not possible, the only solution may be to purchase the material in smaller container sizes, if these are available. When using polyurethanes in mix and dispense machines, it will be necessary to protect both components from moisture, either by fitting desiccant traps to the tanks or by flushing the tanks continuously with dry nitrogen. The isocyanate is the hazardous part of the formulation and should not be heated or sprayed as this will increase the levels in the atmosphere and hence the sensitising effect on the lungs. If the storage temperature of the MDI containing hardener drops below 18°C for a prolonged period (>24 hours), then the hardener may start to crystallise and a white sediment forms at the bottom of the container. Normally this can be redissolved back into solution by heating the material to 40°C for a couple of hours, and the material is fit for use once all the crystals have dissolved. If the crystals do not dissolve, then it is likely that the hardener has got wet over time. If there are two hydroxyl groups on the polyol (a diol), a soft cured product results, hardness can be increased by the addition of a triol (three hydroxyl groups) or tetraol (four hydroxyl groups), this leads to a more cross linked structure when the resin is cured. The molecular weight of the polyol will also impact upon the flexibility of the cured resin. The type of polymer backbone has a large impact upon the chemical resistance of the resin, as well as its toughness and viscosity. It must not be forgotten that there are now an increasing number of bio sourced and sustainable polyols that allow resins to be developed which have a reduced overall environmental impact.
Speed of cure in urethane systems is very easily adjusted by adding increasing amounts of catalyst to the resin component. These catalysts generally fall into two categories, amines and transition metal complexes. Each catalyst has its own curing characteristics within a resin system. Unfortunately the changing nature of legislations, particularly RoHS, REACH and GHS, has meant that certain chemicals have either been restricted in use, banned for certain uses or taken off the market. This has meant that chemists have had to work hard to reformulate existing products to maintain the current properties, as well as developing new products to meet the changing needs of the market.
Silicone resins are based on silicone polymers of various molecular weights, with different terminal groups to provide the required functionality. As with polyurethanes the hardness of the resin can be adjusted by using branched polymers to increase the cross link density of the cured resin. Silicones use a number of different catalysts to initiate the curing process, in many cases these are based on platinum complexes, which can easily be poisoned by trace amounts of other materials, amines are particularly effective at reducing the activity of these catalysts. It is not recommended to cure epoxies and silicones in the same oven. Also depending upon the type of terminal groups (vinyl or hydroxyl) will determine the curing reaction, and if moisture is required. Unlike epoxies, polyesters and polyurethanes, silicones generally cure from the exposed surface down through the body of the resin. This means that the silicone will have a rapid skin time (sometimes called the tack time), but then the curing reaction is progressive through the body of the resin, this means that the depth of the resin will determine the cure time.
Solid fillers are a very important constituent of many resin systems. They can be added to simply reduce cost e.g. powdered limestone. The cost savings are generally slightly less than might be suggested by the cost per kg, as filled systems have a higher density than unfilled ones. This means that whereas a unit might require 3 grams of resin of density 1.0 to fill it, it will require 4.5 grams of a resin of density 1.5. In each case the volume is 3ml. Cost comparisons of competing resins should always be done on a per litre basis, rather than a per kg basis.
The presence of solid fillers will usually give rise to a harder and stiffer cured product. Fillers can be added to act as flame retardants. Alumina trihydrate is commonly used for this purpose: this has the added advantage of resulting in low smoke emission and a low level of toxic fumes. ER 2188 and 2195 are popular examples of alumina trihydrate filled flame retardant epoxies – both are fully approved to UL 94 V-0. UR 5097, 5604 and 5608 are examples of flame retardant polyurethanes utilising the same mechanism for achieving flame retardancy also approved to UL 94 V-0. The disadvantage is that high loadings of alumina trihydrate are required, resulting in a relatively high viscosity formulated resin. Traditionally halogenated compounds have been used as flame retardants. However, their use gives rise to a higher level of smoke and toxic fumes, which have become problematic. Phosphorous based fillers and additives have been used to produce a new generation of flame retardant resins, which emit lower levels of smoke and less hazardous fume. ER2218 and 2221 are example of this type of low viscosity flame retardant epoxy. A new generation of flame retardants of completely different chemical type are now becoming available and are being introduced to the new generation of resins that have been developed.
Many other types of fillers can be used in epoxies, polyurethanes and silicones. Hollow glass and plastic spheres give reduced density and low dielectric loss. When potting RF circuitry the potting resin can introduce capacitance effects between conductors on the printed circuit board and alter unacceptably the characteristics of the circuit. It may be possible to overcome these problems by use of hollow sphere containing resins of low dielectric constant – typical examples of such resins are ER 1448 and UR 5118. Zinc oxide and aluminium oxide give improved thermal conductivity, but aluminium oxide is extremely abrasive and causes severe wear problems in mix and dispense equipment. ER 2183 and 2221 are very popular examples of zinc oxide filled thermally conductive epoxies. UR5608 and SC4003E are examples of a polyurethane and silicone resin respectively that show good thermal conductivity. Silica flour gives lower cure shrinkage and coefficient of thermal expansion but is very prone to sedimentation. Milled glass fibres give improved impact resistance; barium sulphate gives opacity to X-rays etc. etc.
In the early days of potting and encapsulation epoxy resins were the materials of choice. Epoxy chemistry has evolved over the years to meet the changing needs of industry and the regulatory environment, however both polyurethanes and silicones have matured in terms of the resins being developed and offered. However with the changing and evolving electronics market, with the demands of the evolving e-mobility market, the use of LED’s and the natural development and progression of smaller and more powerful components and devices, the market is requiring the development of new resins and materials to meet these requirement. To this end chemists are reaching deep into their cupboards to find materials and chemistries to meet the demands of today and tomorrow.